How Asphalt Paving Works
Asphalt is less expensive than other paving materials, and it’s quicker to install. It can also be colored and stamped to match design preferences, making it ideal for everything from driveways to corporate parking lots.
Smooth roads are safer for travelers, and they reduce vehicle wear and tear that translates to lower maintenance costs. Routine inspections and crack sealing help avoid costly repairs in the future. Contact Asphalt Paving Summerville SC now!
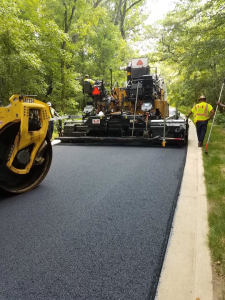
When a new asphalt surface is installed, it must be properly prepared to create a strong foundation and long-lasting pavement. This starts with clearing the area and removing existing pavement materials. This can be done using small to large machinery like bobcats, dump trucks, and front loaders. The soil must then be tested to determine its strength and stability and it must be graded and contoured to ensure proper drainage and prevent water pooling that can damage the pavement over time.
The next step is installing a strong base layer of crushed stone or gravel. This provides a stable foundation and increases the pavement’s load-bearing capacity. Once the base is in place, it must be compacted to ensure consistency and prevent settling and cracking.
Next, the asphalt mixture is prepared in an asphalt plant. The mixture is a combination of aggregate, binder, and filler material and is carefully designed to meet the needs of each project. The most common asphalt mix is hot-mix asphalt (HMA), which is heated to a temperature of 300-350 degrees Fahrenheit. This helps the mix stay warm and flexible, allowing it to be applied in cooler weather conditions. Another type of asphalt is Warm Mix Asphalt, which uses a lower heat level and releases less greenhouse gases into the atmosphere.
The final stage is adding the surface asphalt, which is composed of sand and smaller aggregate mixed with petroleum-based binder, known as bitumen. This is the material you see on roadways and parking lots, and it’s what gives them that shiny, jet-black finish. Once the surface asphalt is laid and compacted, it requires a few days to fully cure and harden.
Mixing
Different applications require different asphalt mixes. Highways and busy city streets demand high-performance mixes that can handle heavy traffic loads and weather conditions, while residential driveways can use a lower-cost mix with lower performance requirements. The optimum asphalt mix for each application is determined by a mix design process. This process determines the aggregate and asphalt binder to be used and identifies the optimum combination of these ingredients. The resulting mix design is typically referred to as a job mix formula (JMF) or recipe.
Generally, the mix design for HMA begins with evaluation and selection of a number of different aggregate sources. Each source is evaluated with a battery of physical tests and must meet specific gradation requirements. Once the appropriate aggregate is selected, it is combined with asphalt binder in an asphalt mixing plant. The mixture is heated to a specified temperature to facilitate the coating of the aggregate with asphalt and to remove any moisture. The mixture is then ready to be transported to the construction site.
One variation on traditional HMA is warm-mix asphalt (WMA). This type of mixture is produced by using processes or additives that allow the production and placement of asphalt binders and aggregate at temperatures (30-100oF) lower than conventional HMA without sacrificing performance. Some WMA technologies reduce the viscosity of asphalt binders so they can coat aggregates at lower temperatures. Others hold internal moisture in the mixture to create a foamed binder and provide easier manipulation and compaction during placement.
Another variation on HMA is stone-matrix asphalt (SMA). This type of mixture is characterized by having a large number of intermediate size aggregates that are missing or present in small amounts. This type of mix is characterized by stone-on-stone contact, making it more permeable than dense-graded or open-graded mixtures.
Applying
Asphalt is a versatile material that can be used in a variety of ways. It is durable, cost-effective, and offers a polished aesthetic that can be customized to suit the specific needs of each project. It is also safe and comfortable for drivers, with excellent traction and reduced noise levels.
The first step in the installation process is to prepare the surface. This involves grading and shaping the base to achieve a smooth, stable structure. This foundation supports the load-bearing properties of your asphalt pavement, and is essential for its longevity.
Once the base has been laid down and any soft areas of the base repaired, it’s time to apply the binder layer. This consists of a mixture of aggregate and oil that will help support your asphalt and ensure it lasts for years to come.
In this phase, it is important to follow the specified asphalt mix design, which takes into consideration factors like climate and traffic volume. This is to guarantee that the asphalt will be strong and sturdy enough to withstand environmental elements, heavy vehicle loads, and other external forces.
Typically, the base and binder layers are made from hot mix asphalt (HMA). This is produced at high temperatures for maximum durability and long-term performance. However, cold mix asphalt is also an option, which can be produced at lower temperatures for energy efficiency and sustainability.
Once the base and binder layers are applied, the final layer of asphalt is laid on top. It is crucial that this is done correctly to ensure a high-quality finished product. It is best to apply a thick lift of asphalt, ensuring that it is rolled and compacted at least three or four times the nominal maximum aggregate size (NMAS) of your chosen asphalt mix. Doing this will improve mat density and aeration, which helps reduce cracking, water intrusion, and fatigue over time.
Compaction
Compaction is the process of removing air from your asphalt mixture, resulting in a stiff and durable pavement. It begins behind the scenes, when the hot mix is produced at the plant and kept at a constant temperature until it’s ready to be transported and delivered to your site. Asphalt teams have to keep a close eye on the temperature of your asphalt throughout the paving process, making sure that it remains in the correct temperature zone. Once it is on the job site, contractors use different types of equipment for compaction. These include a double drum vibratory roller, pneumatic tire roller and static steel wheel roller. Knowing how these machines work and the best rolling pattern to use is important for achieving your desired target density.
The compaction of your asphalt is the most crucial step in the paving process. It’s vital that your contractor is experienced and pays attention to detail. They should have a good understanding of the primary factors that influence the time available to compact the asphalt mixture – such as air temperature, base temperature, mix laydown temperature, layer thickness and wind velocity.
A common mistake is for the paver and rollers to stop operating together, which causes the mix to cool before it’s able to be properly compacted. The best way to avoid this is to create a “rolling train,” which involves multiple rollers that operate one after another close behind the paver.
The shear stress created by the different rollers compresses the asphalt mixture, causing it to get into a more dense configuration. This reduces future soil settlement and helps to eliminate deleterious shrinking and swelling properties that can compromise the integrity of your pavement structure.
Curing
Optimal asphalt curing is crucial for long-lasting, durable pavement. Proper compaction is an important factor, as it eliminates the air voids that would otherwise slow down asphalt curing. This process also boosts your mix’s stability, strength, and load-bearing capacity. The most important thing to remember is to allow a minimum of 14 days for your new asphalt to fully cure. Using it too soon risks indentations, scarring, and other damage to the surface.
The ideal weather conditions for laying asphalt are warm, dry, and sunny. In these conditions, the asphalt’s moisture can evaporate quickly, shortening its curing period. However, inclement weather such as rain or humidity introduce complications that impede the evaporation of moisture and prolong your asphalt’s curing time.
When your asphalt is sufficiently cured, it will have a firm, non-sticky texture and will no longer emit a strong odor. It will also be able to withstand light traffic. However, it’s still best to avoid driving on it until it has completely cooled and cured. Parking on a newly paved surface too early can cause irreparable damage to your asphalt, such as tire dents and power steering tears (the scraping up of sections of the asphalt by the movement of wheels and other mechanical equipment).
If you want to reduce the duration of your asphalt’s curing time, ask your contractor about specific techniques they use to speed up the process. These methods often involve the use of curing compounds that form a protective seal on your asphalt’s surface and accelerate its drying process by facilitating vaporation. Taking advantage of these techniques can help your asphalt reach full curing in as little as three days instead of the usual six to twelve months.